With the market increasingly headed in these three directions, the company from Vigevano, leader in the production of cutting systems, reconfirms these trends, presenting three innovations destined to optimise productive processes and increase productivity
While the post-pandemic world accelerates with regards to environmental protection and digital technologies, Atom Group reconfirms the trends underway in the market by presenting three solutions for the automation and digitalisation of productive processes at Simac, while looking with attention at all the aspects of sustainability. The products involved are the new FlashCut Master 2185 cutting system, the Sincron HR hydraulic toe lasting machine, and the CD15 VRX cementing machine. As one of the most innovative and versatile cutting systems of the Atom range, FlashCut Master 2185 is in fact capable of cutting both leather and synthetic materials and includes VRX technology that recognises printed materials and logos. The double-pincer systems with removable mobile pincer allows multilayer materials to be cut, while the automatic setting of the cutting head allows for less wear of the cutting belt. Its flexibility makes it perfect for use in different industrial sectors like footwear, leather goods, furniture, and automotive.
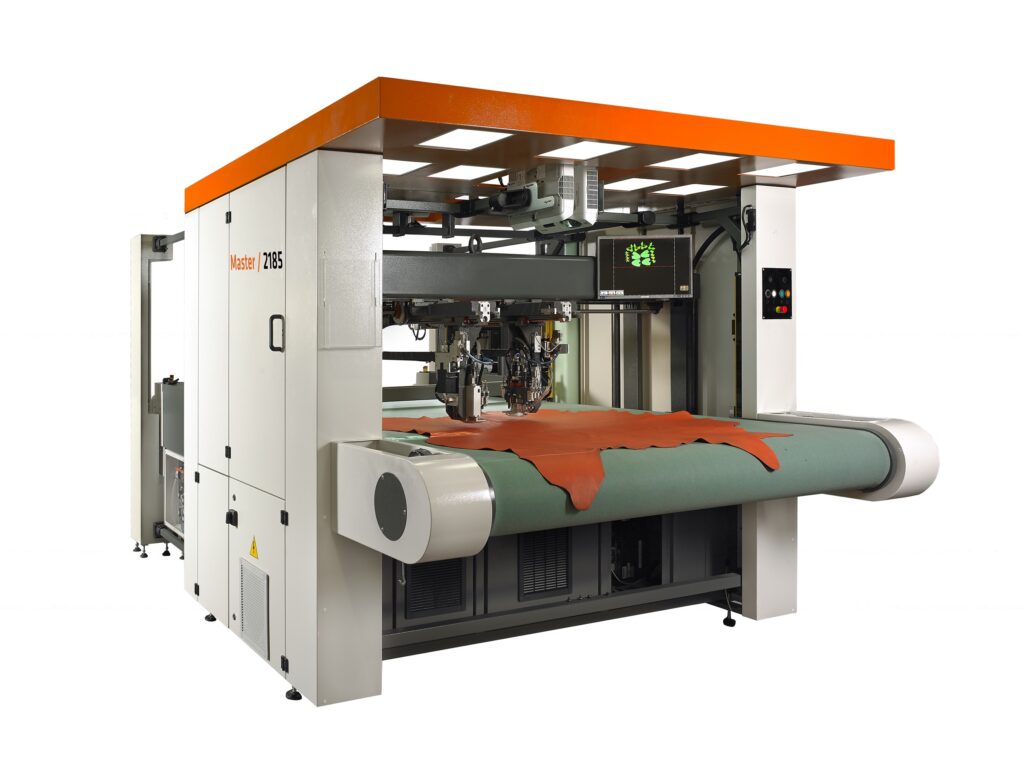
Brand new for Atom is the Sincron HR hydraulic toe lasting machine intended for large series production, which was developed together with Reces, a historic company with 60 years of experience in the industry, completing the new Sincron series of machines produced by this Vigevano company. Sincron HR combines state-of-the-art technology with reliability and ease of use.
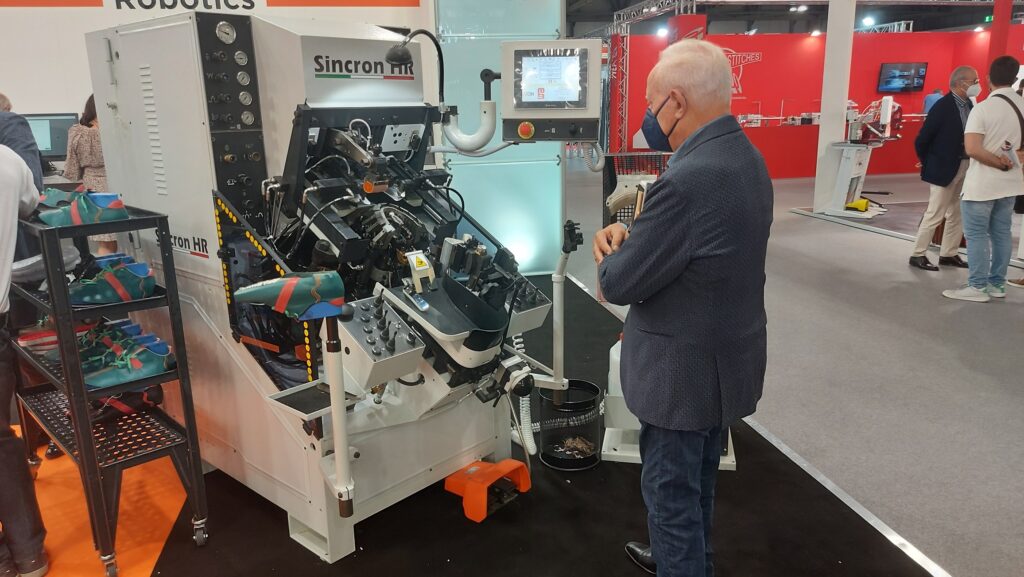
Finally, for the cementing phase, the most up-to-date solution presented by Atom at Simac is represented by the CD15 VRX robotic cementing machine, which is capable of processing any type of sole, including even the most complex. Equipped with a rotary table with 3 positions, this machine is capable of working 2 soles simultaneously, thereby guaranteeing high productivity. The gluing path is defined through 3D scanning, eliminating the need for programming.
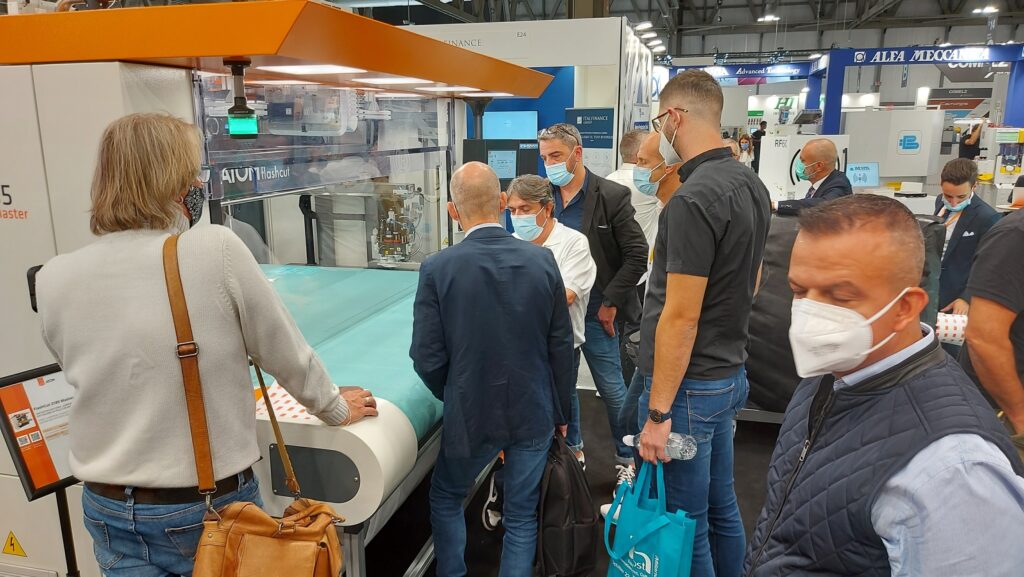