Seven innovative patents registered in just a few years. This is the business card of PL Project, which has years of experience in the fashion accessories industry and has revolutionized edge dyeing of leather products.
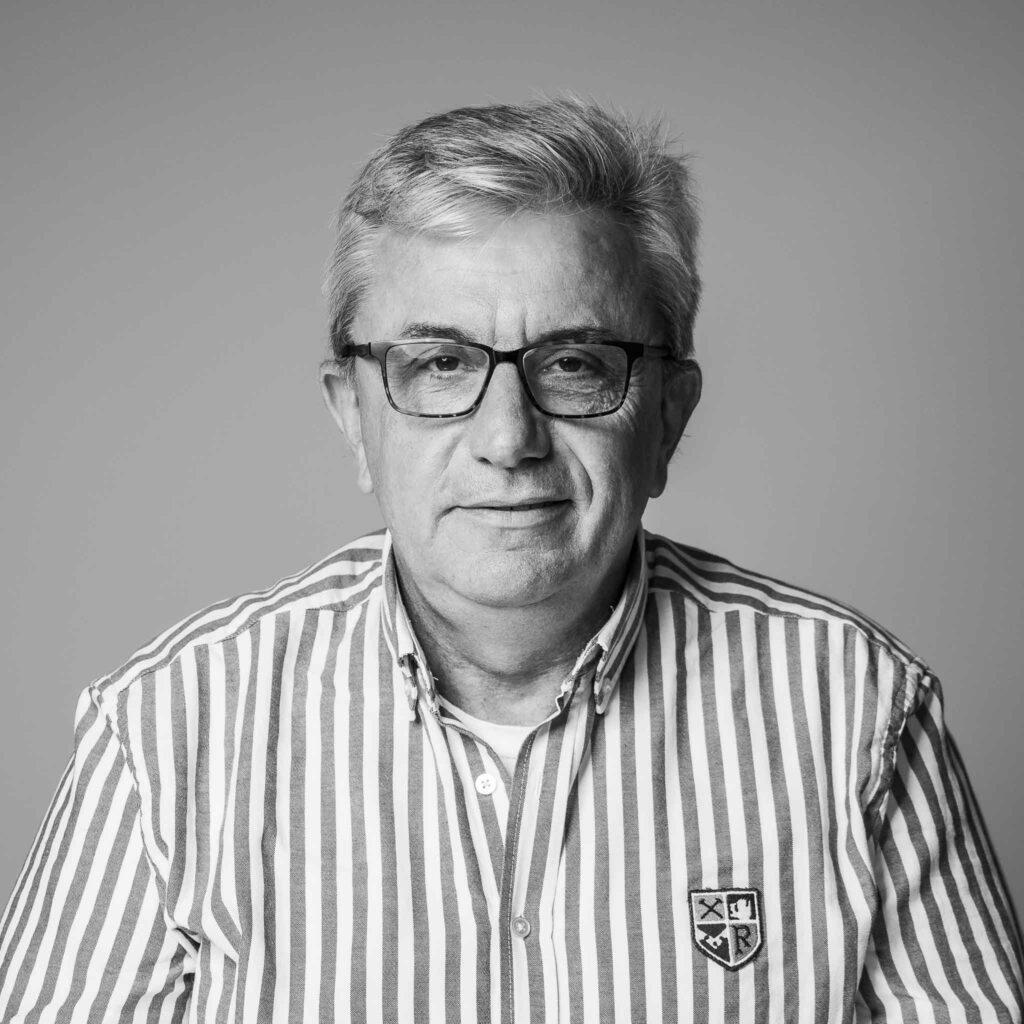
PL Project was born as the rib of a bag-making factory, Prolet Ltd, which has been in the industry for more than 55 years. This is a factor not to be overlooked and clearly indicates that the more than 20 engineers working at PL Project know precisely the requirements of a handbag or production line. What’s more, they have the opportunity to field test new technologies before launching them on the market. This allows the machines produced by PL Project to be not only technologically innovative, but also extremely easy to use, as well as reliable.
Since 2016 PL Project has grown significantly and today has extended its representative network to 6 countries: Italy, Romania, Spain, France, Portugal and the United States.
It is Plamen Tzonev, CEO of PL Project, who explains why the company is a consistent partner for bringing innovation to manufacturing companies. “Our mission is to make automated systems and machines for the footwear and leather goods industry that are not yet available on the European and world markets. It is with this goal in mind that engineers and software developers, strengthened by the work and experience gained at the Prolet factory, have begun to create absolutely innovative technologies, such as automated dyeing, spraying and drying units for leather details, production lines that are also automated, including non-contact transport trolleys for blanks, and many other related machines and software.”
Your patents have revolutionized the world of edge coloring for leather parts. What are the most innovative aspects of your technology?
“Our edge dyeing systems offer an experience that was unthinkable until recently: the ability to effortlessly change up to 5 colors in seconds using a single machine.
Added to this is the exceptional precision in adjusting the amount of paint. Ours are the only machines that allow adjustment in ten steps, each of 0.075 mm for a total rotation from 0 to 10 of 0.75 mm.”
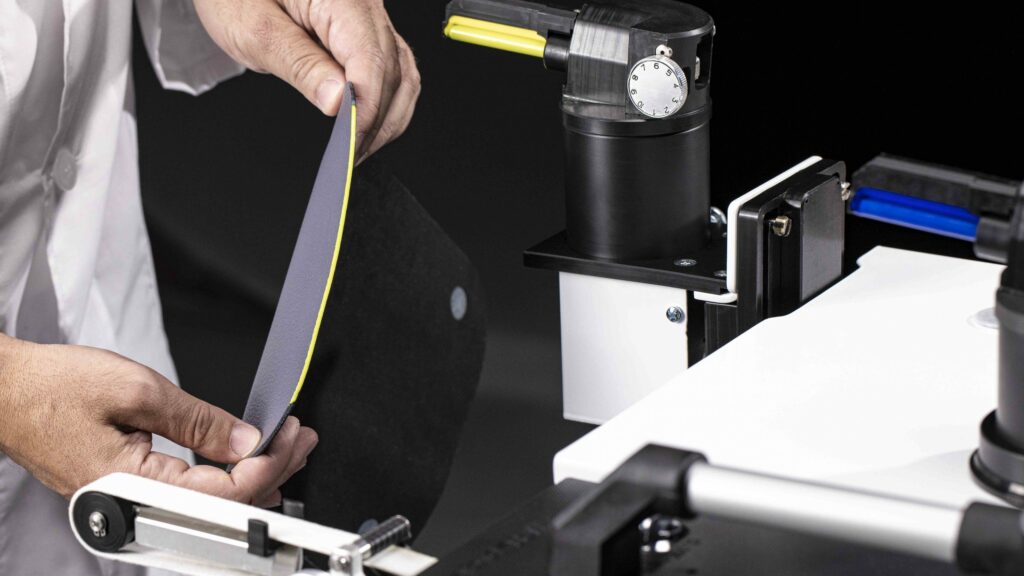
What insight enabled you to achieve such results?
“To have focused on a magnetic transmission from one module to another of the drive parts. Thus, we were able to use several modules on the same machine that engage with each other quickly and easily. We turned a single dyeing machine into a complete system for leather edge coloring.”
What makes this technology further unique?
“The quick head change in one movement thanks to the special container gripping system. The possibility of not stopping the workflow and the ability to close the head cap so the paint is preserved from drying out or evaporating.
Cleaning the heads is quick and easy. They consist of only 8 parts that can be disassembled quickly and easily at the end of the day.
The washing module that ensures a perfect finish since it can remove even the smallest imperfections resulting from the edge painting process.
And, finally, the 5 coating heads, both horizontal and vertical, which allow any product to be dyed and 5 different colors to be used, albeit in a machine with compact and modular dimensions that allow it to be placed practically anywhere.”
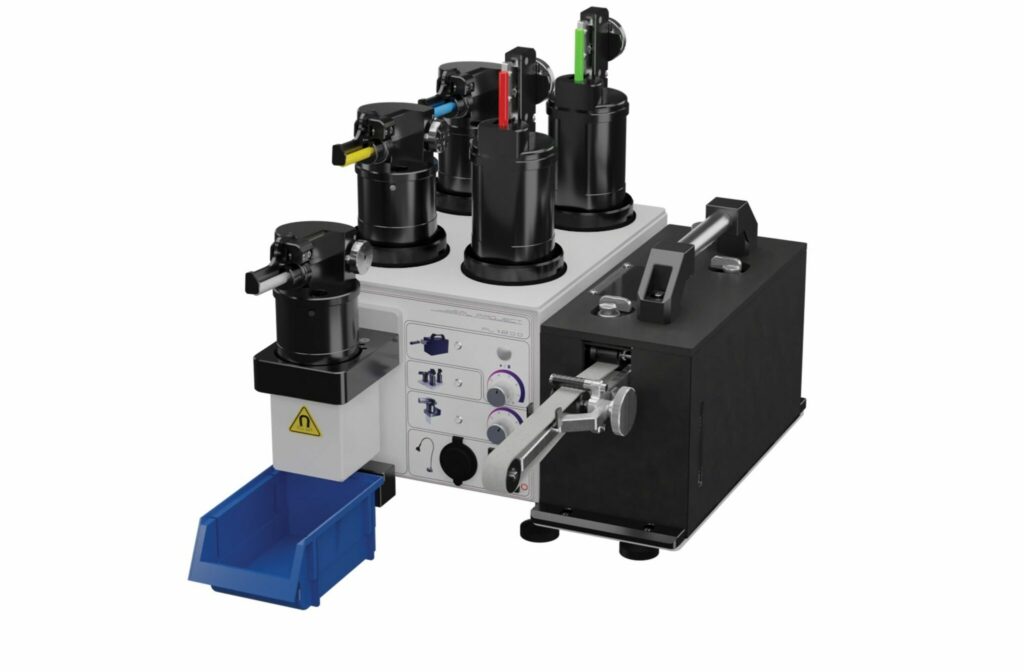
The topic of energy efficiency is so important. How did you manage the consumption of your system?
“We created the Blue Planet Line. An innovative low-voltage system that powers very efficient electric motors. Our machines consume so little electricity that they can be powered by a simple, common power-bank, perhaps recharged at night, when energy is cheaper. For example, our dyeing machine mod. BPL1310 from the Blue Planet Line consumes only 2.5 W while similar machines from other manufacturers consume no less than 300 W”.
What made this concentrated technology possible?
“Having developed all the components that make up the system in-house, starting with the power supply for the machines, passing through the electric motors and ending with the use of the best possible technology for edge dyeing.”